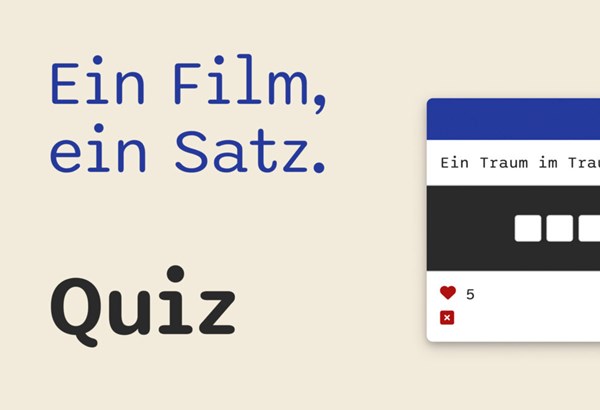
Begonnen hat alles mit Müll. Genauer gesagt mit «thermoplastischen post-consumer Kunststoffabfällen». So werden die Kunststoffverpackungen genannt, die von uns Konsumenten gekauft und meistens sofort wieder weggeworfen werden. Laut dem vor zwei Jahren erschienenen Bericht der Ellen MacArthur Foundation landen von den weltweit jährlich produzierten Kunststoffverpackungen 72% in der Natur oder auf Deponien. Das ist eine ziemlich grosse Menge Kunststoffabfall, wenn man bedenkt, dass jährlich 78 Millionen Tonnen produziert werden (1).
Als Industriedesigner faszinierte uns die Idee, aus diesen Kunststoffmassen ein sinnvolles Produkt zu gestalten. Denn thermoplastische Kunststoffe sind sehr divers einsetzbare Werkstoffe und deshalb auch eine wertvolle Ressource. In diesem Sinne könnte man eine Abfalldeponie mit einer Goldgrube vergleichen. Doch welche sinnvollen Produkte liessen sich aus diesem «Gold» herstellen?
Wir wollten ein Produkt gestalten, das einen positiven Einfluss auf Menschen und deren Leben haben kann. Da sich viele der oben erwähnten Deponien in sogenannten «Less Developed Countries» (LDC’s) befinden, haben wir in deren Kontext nach potentiellen Projekten gesucht. Die Recherche hat gezeigt, dass die Nachfrage nach günstigen Beinprothesen in vielen LDC’s sehr hoch ist. Hauptursachen sind die oft fehlende medizinische Grundversorgung, Verkehrsunfälle und gewalttätige Konflikte oder Kriege. Die Weltgesundheitsorganisation schätzt, dass weltweit 35 Millionen Menschen eine Prothese oder Orthese benötigen (2). Somit hatten wir die Anwendung für das Kunststoffgold gefunden, wie wir sie uns vorgestellt haben: Eine Beinprothese kann das Leben von Menschen und deren Umfeld positiv verändern, indem sie ihnen das Gehen wieder ermöglicht. Dies war die Geburtsstunde von «Project Circleg».
In den darauffolgenden drei Monaten haben wir uns intensiv mit der Weiterentwicklung der Idee einer kostengünstigen Beinprothese aus rezyklierten Kunststoffabfällen beschäftigt. Begonnen haben wir mit einer breiten Recherche in den Bereichen der Prothetik und der Kunststoffabfallindustrie. Wir teilten unsere Idee mit verschiedenen Orthopädietechnikerinnen und Materialexperten, um uns einerseits eine Wissensbasis für das Projekt zu schaffen und andererseits unsere Idee einem Reality-Check zu unterziehen: Was denken die jeweiligen Experten über unser Vorhaben? Das Fazit: Die Thematik ist extrem komplex, das Potenzial der Idee jedoch durchaus hoch. Denn bestehende Prothesensysteme weisen oft funktionale Mängel auf, sind von Materialimporten abhängig oder für die Betroffenen schlichtweg zu teuer.
Im März 2018 reisten wir nach Kenia um Einblicke in bestehende Prothesenprojekte sowie in lokale Kunststoffabfallverwertungsindustrien zu erhalten. Zudem wollten wir uns mit den wichtigsten Experten der low-cost Prothetik austauschen: den Menschen, denen ein Bein amputiert wurde. Wir lernten ihre Erfahrungen und Ansichten kennen, ihre alltäglichen Herausforderungen und Bedürfnisse und wir konnten gemeinsam mögliche Lösungsansätze diskutieren. Ein Beispiel für solche Herausforderungen sind Hocktoiletten, welche oft in ländlichen Gebieten Kenias vorkommen und für deren Benutzung eine kauernde Position eingenommen werden muss. Dies ist mit den bestehenden Prothesen jedoch nicht möglich und die Betroffenen müssen vor jedem Toilettengang die Beinprothese ausziehen.
Uns war es wichtig, solche Erkenntnisse in die Entwicklung und Gestaltung eines neuen Prothesensystems einfliessen zu lassen und eine funktionale Lösung für dieses Problem zu finden. Dafür haben wir unzählige Funktionsmodelle gebaut, die wir mit einer eigens dafür konstruierten Halterung selbst getestet haben. Die Herausforderung bestand jedoch darin, ein Prothesensystem zu entwerfen, das mit den geringsten finanziellen Mitteln die höchstmögliche Funktionalität bietet. Nach einem intensiven und sehr iterativen Designprozess haben wir am 7. Juni 2018 den ersten Prototypen des Circlegs an der Diplomausstellung im Toni Areal ausgestellt.
Das Circleg haben wir für Ober- und Unterschenkelamputierte entwickelt. Es ist vollständig modular aufgebaut und besteht aus zwei Adaptern, einem Kniegelenk, einer Pilone und einem Fusspassteil mit arretierbarem Gelenk. Die zwei Adapter ermöglichen die individuelle Anpassung der Beinprothese an den Körper des Benutzers. Das Knöchelgelenk erlaubt eine kauernde Haltung und damit auch die Benutzung einer Hocktoilette, ohne dass die Beinprothese ausgezogen werden muss. Um gefährliche Stolper zu vermeiden, ist das Kniegelenk mit einem Mechanismus ausgestattet, der das Bein beim Gehen nach vorne schwingt. Zudem schützt eine Gelenkkappe vor Schmutz und ermöglicht eine kniende Position. Das Circleg wird aus recyceltem Polypropylen (PP) hergestellt, welches mit Glasfasern verstärkt wird, um einen Verbundwerkstoff zu schaffen, der den Hochleistungsanforderungen einer Beinprothese gerecht wird.
Unsere Vision ist es, den Menschen, die sich bis anhin keine Beinprothese leisten konnten, wieder das Gehen zu ermöglichen. Dafür wollen wir ein ökologisch, wirtschaftlich sowie sozial nachhaltiges Geschäftsmodell für die Herstellung einer low-cost Beinprothese entwickeln. Durch die Verwendung von rezyklierten Kunststoffabfällen als Material in Kombination mit vor Ort bestehenden Produktionsmethoden soll das Circleg lokal und kostengünstig hergestellt werden. In einem HUB, einem Treffpunkt oder Zentrum, soll die individuelle Anpassung der Beinprothese an den Benutzer stattfinden. Zudem werden dort Passteile mit lokalen Mitteln und vorhandenem Know-how repariert oder ausgetauscht. Verbrauchte Passteile werden wieder rezykliert und in den Materialkreislauf zurückgeführt.
Aktuell sind wir auf der Suche nach Finanzierungsmöglichkeiten, damit wir den Prototypen weiterentwickeln und erste Tests durchführen können. Wie die Geschichte weitergeht, darüber berichten wir nächstes Mal.
(1) McArthur Foundation, Ellen. 2016. The new plastics economy. Rethinking the future of plastics.
(2) World Health Organization (WHO). 2018. Global Disability Summit 2018 London